Tracks
Documentation and Assembly Insructions for the FarmBot Genesis Tracks
- Assembly Instructions
- Step 1: Gather the Parts and Tools
- Step 2: Layout the Track Extrusions
- Step 3: Attach a Track End Plate
- Step 4: Attach a Track Joining Plate
- Step 5: Attach the first Track Extrusion
- Step 6: Attach the second Track End Plate and Extrusion
- Step 7: Add a short cable carrier mount
- Step 8: Add cable carrier supports
- Troubleshooting and Maintenance
- Change Log
- Room for Improvement
FarmBot’s tracks allow the gantry to move in a precise motion along the x-axis. The tracks are designed to attach to a raised bed or similar supporting infrastructure. Standard tracks are 3m in length, though one could extend them indefinitely by adding more extrusions and connecting plates.
Assembly Instructions
2 hours
This is the estimated time it will take to assemble the tracks.
Supporting Infrastructure Required
These assembly instructions assume that you already have supporting infrastructure in place, such as a raised bed.
Step 1: Gather the Parts and Tools
Gather all the parts from the table below and lay them out in a logical manner. To complete the assembly, you will also need the following tools:
- 3mm allen (hex) wrench
- Number 2 phillips screwdriver or electric drill with a Number 2 phillips driver bit
Qty. | Component |
---|---|
4 | Track Extrusions |
4 | Track End Plates |
2 | Track Joining Plates |
20 | 1 inch #2 Phillips Wood Screws |
30 | M5 x 10mm Screws |
28 | Tee Nuts |
2 | M5 Locknuts |
1 | 1m Cable Carrier |
1 | Cable Carrier Mounting Bracket |
10 | Cable Carrier Support Brackets |
2 | 5m GT2 Timing Belt |
Step 2: Layout the Track Extrusions
Lay out all of the track extrusions in the location that you want to attach them to your supporting infrastructure. Make sure that extrusions are fully butted against each other. This will help you attach the plates in the correct location.
Overhang is a-ok
The ends of your tracks do not have to match up perfectly with the ends of your supporting infrastructure. A little overhang or coming up short is just fine.
Step 3: Attach a Track End Plate
Position a track end plate as shown below and screw it into the supporting infrastructure with three wood screws. Ensure that the plate is vertically aligned.
Leave room for the gantry
The bottom of the track extrusions must be elevated a minimum distance of 25mm from the top of the supporting infrastructure so that the gantry’s lower V-wheels can move along the bottom of the tracks.
Position your track end plates such that when the track extrusions are attached, there is at least 25mm of clearance.
Lightly screw three M5 x 10mm screws and tee nuts to the track end plate. Orient the tee nuts horizontally.
Step 4: Attach a Track Joining Plate
Position a track joining plate such that one half of it will be able to attach to each track extrusion and so that it is the same height as the first track end plate. Screw it into the supporting infrastructure with four wood screws. Ensure that the plate is vertically aligned.
Lightly screw four M5 x 10mm screws and tee nuts to the track joining plate. Orient the tee nuts horizontally.
Step 5: Attach the first Track Extrusion
Lift the track extrusion up and position the lower V-slot onto the tee nuts of the track end plate.
Lightly tighten one of the M5 x 10mm screws using the 3mm hex driver to prevent the extrusion from falling off, while still allowing it to move loosely.
Lift the other end of the track extrusion up and position the lower V-slot onto the tee nuts of the track joining plate. Verify that the track extrusion is positioned correctly, and then tighten all five of the M5 x 10mm screws that hold it in place.
Step 6: Attach the second Track End Plate and Extrusion
Follow the instructions in Steps 3 and 5 to attach the second track end plate and second track extrusion.
Extrusion alignment is key
Position your track extrusions tightly together at the middle of the track joining plate. The top and bottom of the extrusions must be flush so that the gantry can move across the tracks smoothly. Ensure that your extrusions are parallel (no kink where they meet) by looking down the length of the tracks. If there is a kink, adjust the track extrusions and plates accordingly.
See the gap in the track extrusions? You don’t want that!
For Longer Tracks...
If you are installing more than two extrusions worth of tracks, then repeat the steps 4 and 5 with more track joining plates and extrusions.
Step 7: Add a short cable carrier mount
Insert two M5 x 10mm screws into a short cable carrier mount and lightly screw on two M5 tee nuts.
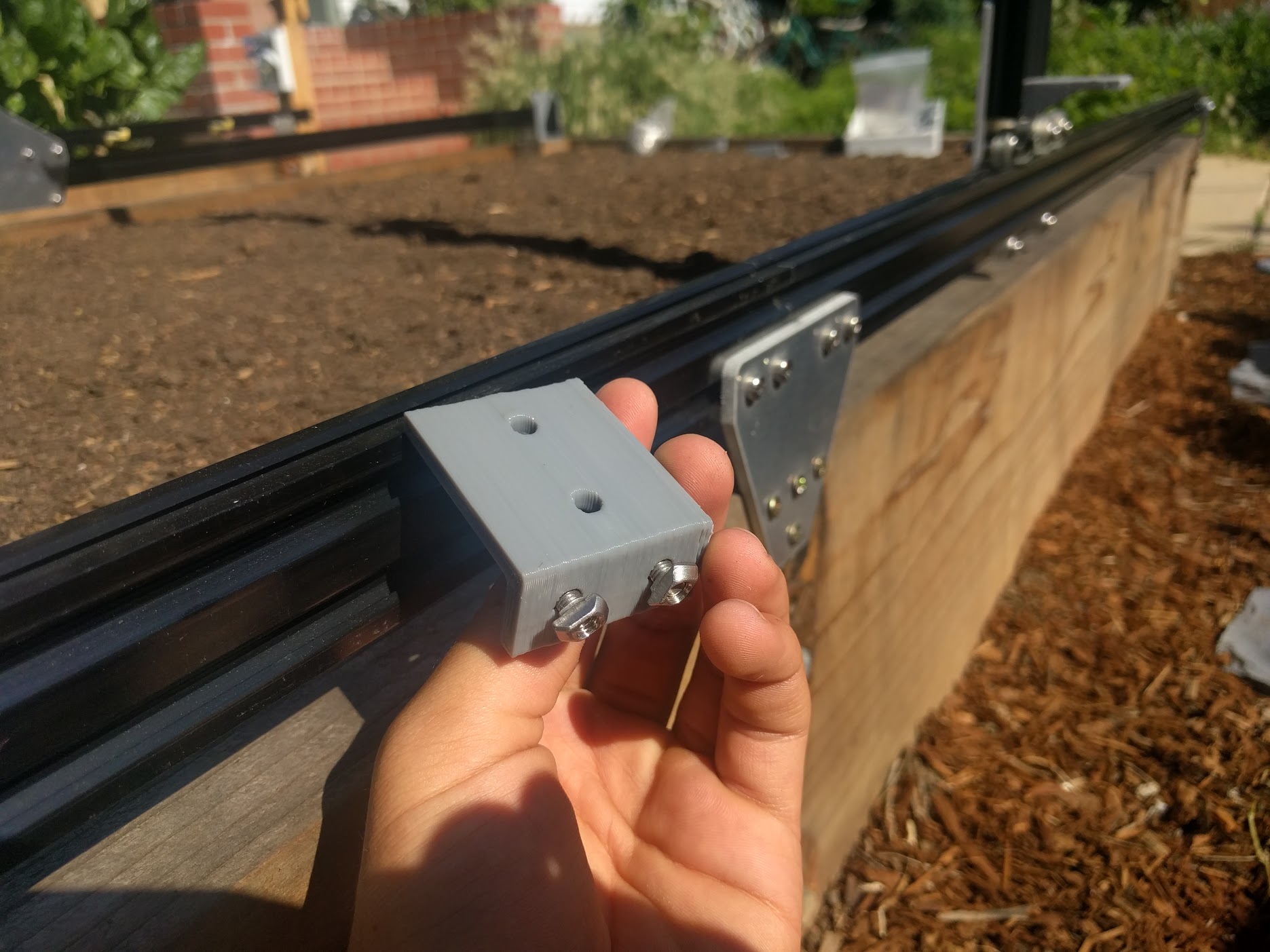
Note that this photo was taken from the back-side of FarmBot.
Place the assembly into the lower slot of the left side tracks. It should be butted up against the track joining plate. Use the 3mm driver to tighten the screws.
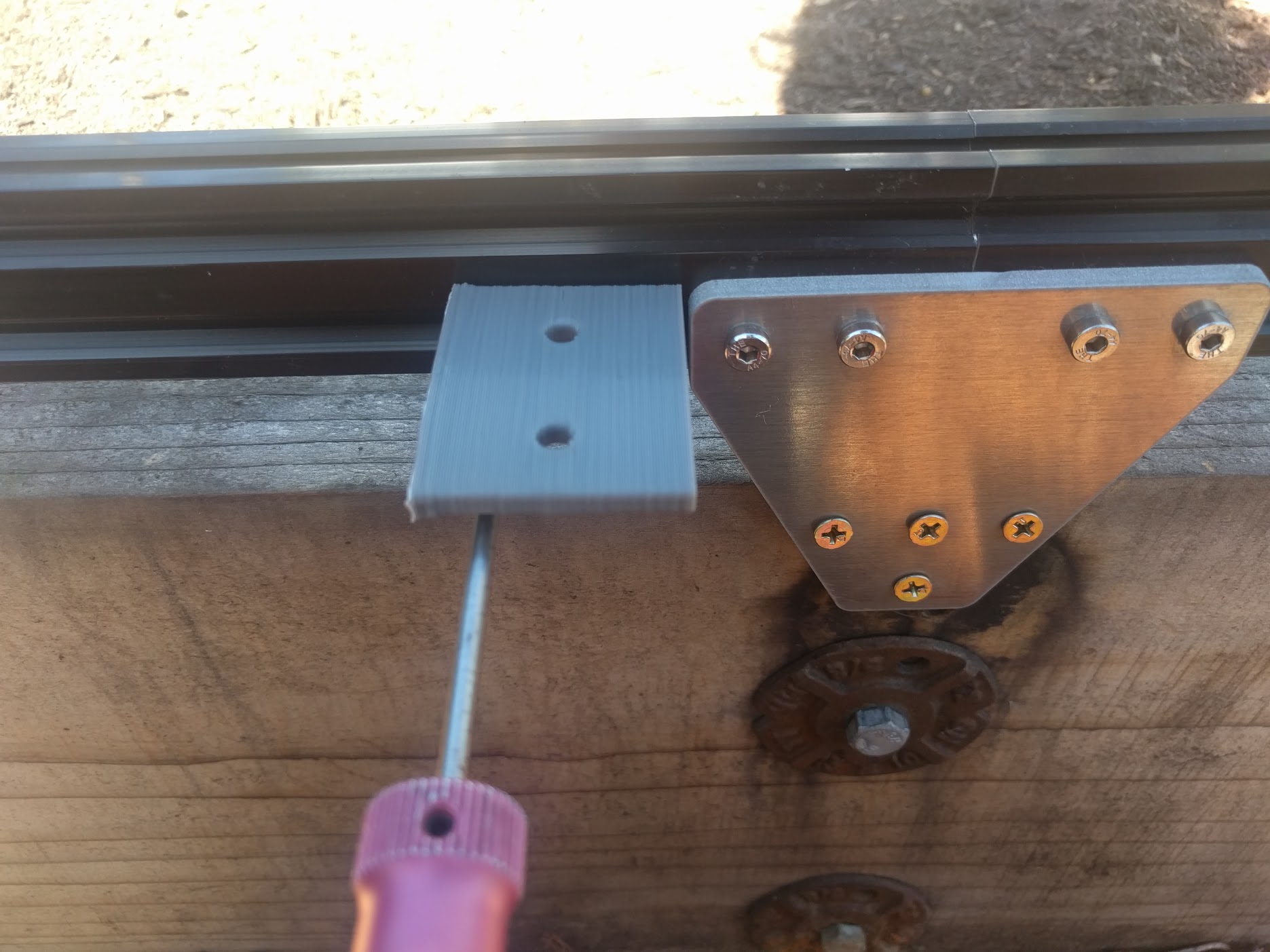
Step 8: Add cable carrier supports
Position the 11 cable carrier supports evenly along the tracks. Keep in mind that the short cable carrier mount acts as a support, so there will be 12 total components supporting the cable carrier. There should be six on each track extrusion.
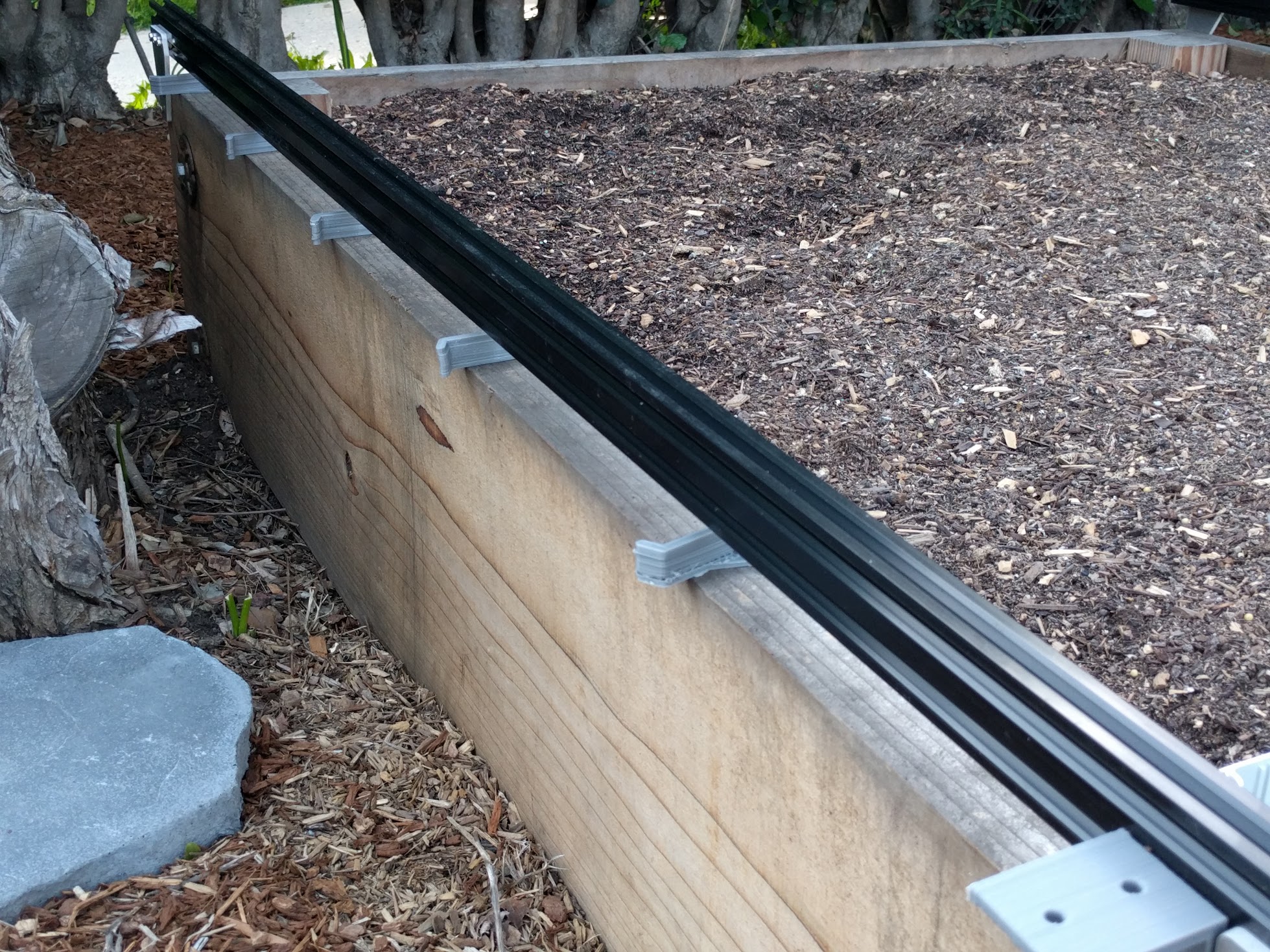
Insert an M5 screw into the cable carrier support and lightly attach an M5 tee nut.
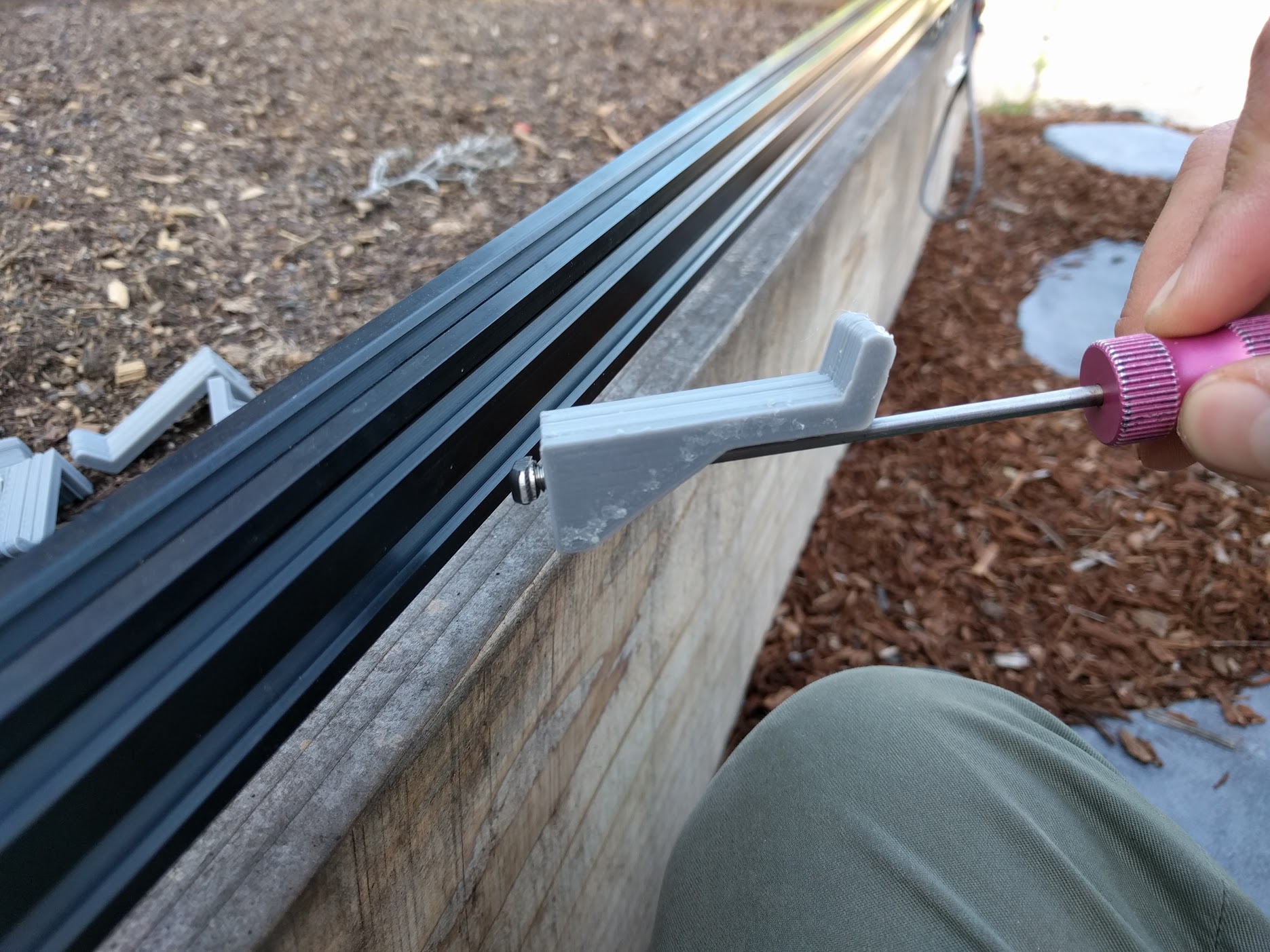
Then use the 3mm driver to tighten the assembly into the lower slot of the track extrusion.
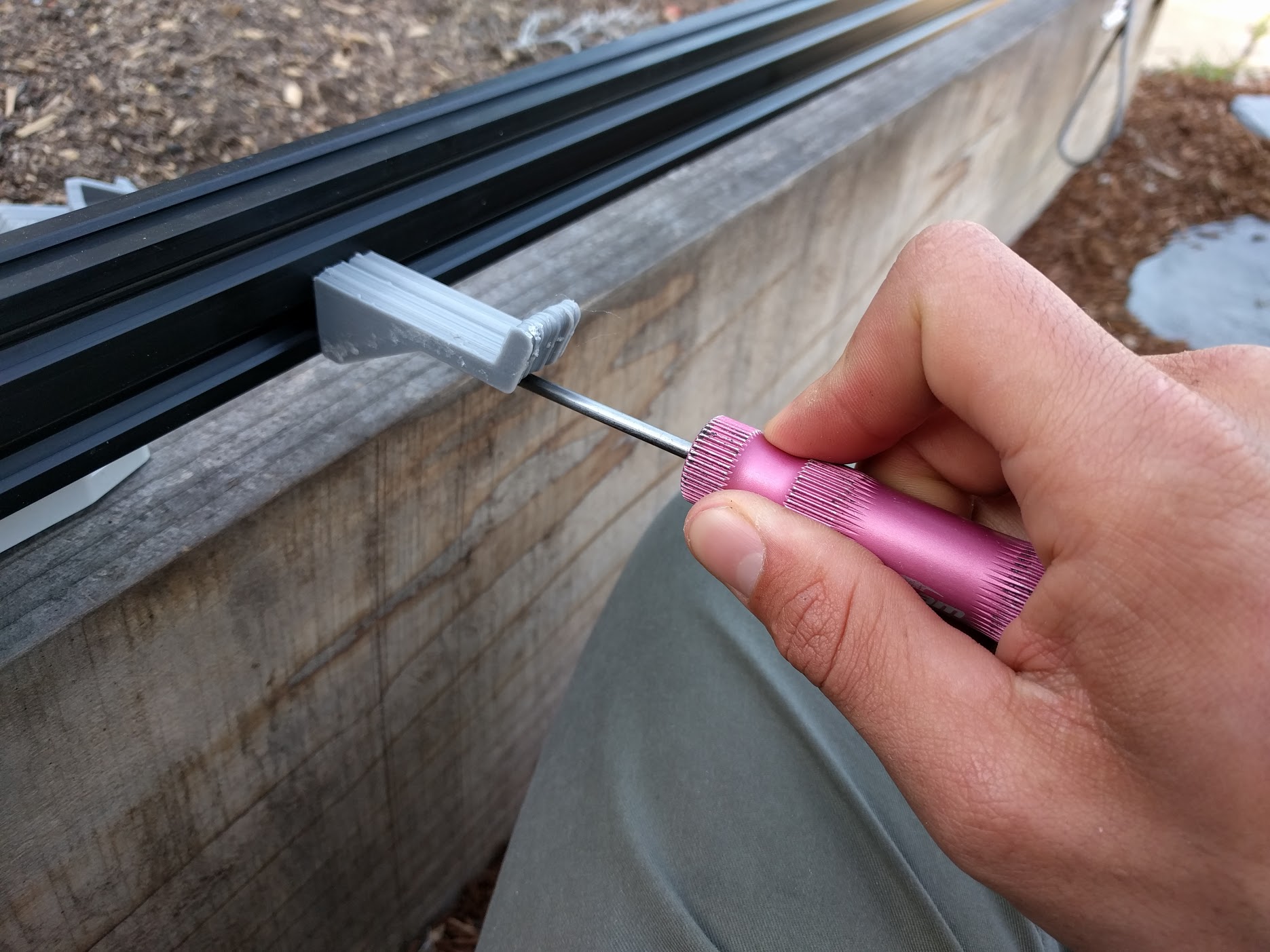
Repeat for all 11 cable carrier supports.
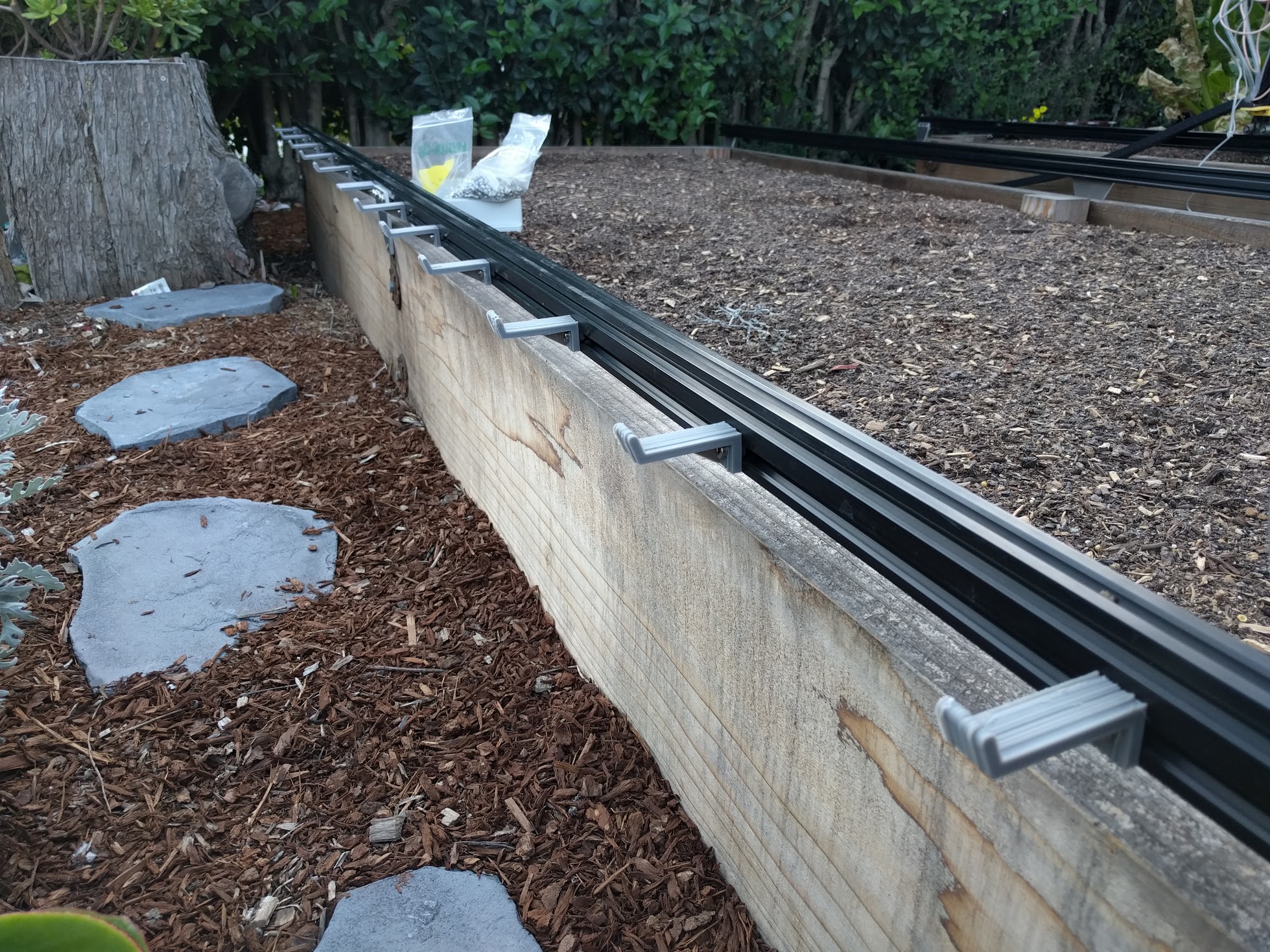
Woo hoo!
You’ve just finished installing your FarmBot’s tracks - arguably one of the most difficult parts of setting up your device. The rest of this page contains valuable information that you should read now or as soon as you’re done assembling the rest of your FarmBot.
Onward!
Troubleshooting and Maintenance
FarmBot’s tracks need to be very straight and parallel with each other in order for the gantry to move smoothly across them. With time, your FarmBot’s tracks may move and twist due to a variety of factors such as:
- Screws becoming loose
- Thermal expansion and contraction due to large temperature swings
- Deterioration of supporting infrastructure such as wood posts
- Supporting infrastructure shifting due to soil expansion and contraction
- Falling branches, earthquakes, or other cataclysmic events
Misaligned tracks can cause the system to creak and ultimately bind as the gantry attempts to move across the tracks. This can prevent FarmBot from working and even cause damage to other components. If you notice your tracks have become misaligned, work to fix them as soon as possible.
Don't forget about General Maintenance!
This section is specifically for track maintenance and troubleshooting techniques. It is to be used in addition to our General Maintenance tips and techniques.
Clean Track Surfaces
Once a month, inspect your tracks for an accumulation of mud, dirt, and other debris. Because the tracks are so low to the ground, it is common for them to accumulate unwanted materials. This can cause your gantry unnecessary friction when moving across the tracks, ultimately leading it to bind up if the tracks are not cleaned.
Regularly
Use a brush, broom, sponge, compressed air, and/or hose to clean the surfaces of your tracks.
Be gentle
Do not apply excessive force in order to avoid misaligning extrusions or bending plates.
Realigning Track Plates
Over time your track plates may become misaligned due to shifting supporting infrastructure or a rare impact event such as a tree branch falling onto the tracks. Signs of a misaligned track plate include misaligned track extrusions (see below), twisted track extrusions, difficulty in the gantry moving across extrusion joints, and even visual misalignment.
To realign track plates...
Try loosing their screws and re-tightening them. You may need to insert a washer or other shim in between the track plate and supporting infrastructure to adequately tighten the plate while maintaining alignment.
Realigning Track Extrusions
It is possible for a track extrusion to loosen and then become misaligned with an adjacent extrusion. Even small misalignments can prevent the gantry from smoothly moving across. Inspect for misalignment by running your fingers across track joints.
Smooth to the touch
If you can feel one extrusion noticeably higher than another, then loosen the M5 screws attaching it to the track plate, realign the extrusion by hand, and re-tighten the screws.
Change Log
- Plates were designed to be larger with more connection points for stronger and more rigid connections to the track extrusions
Room for Improvement
- The track plates are attached to the raised bed with three wood screws. Because the tracks must provide enough clearance between the raised bed and the track extrusions for the gantry’s lower wheels, the track plates need to be positioned so high that the upper wood screws have very little material to screw into. The height of the track plates should be increased so that there doesn’t need to be a compromise between clearance and wood screw connection.
- Assuming the raised bed infrastructure is straight, the track plates need to be positioned at the same height relative to the raised bed. You could do this with a measuring tape or ruler and marking off the location for each plate, but that is cumbersome because it adds extra assembly steps/instructions and tools. A solution is to design into the track plates a marking for the optimal height of the track plates or two marks for the minimum and maximum height.