Tracks
Documentation and assembly instructions for the FarmBot Genesis tracks
FarmBot’s tracks allow the gantry to move precisely along the x-axis. They are designed to attach to a raised bed or similar supporting infrastructure. Each track is composed of 1.5m long aluminum extrusions positioned end-to-end to form a total track length of 3m for Genesis models, 6m for Genesis XL, and 18m for Genesis MAX.
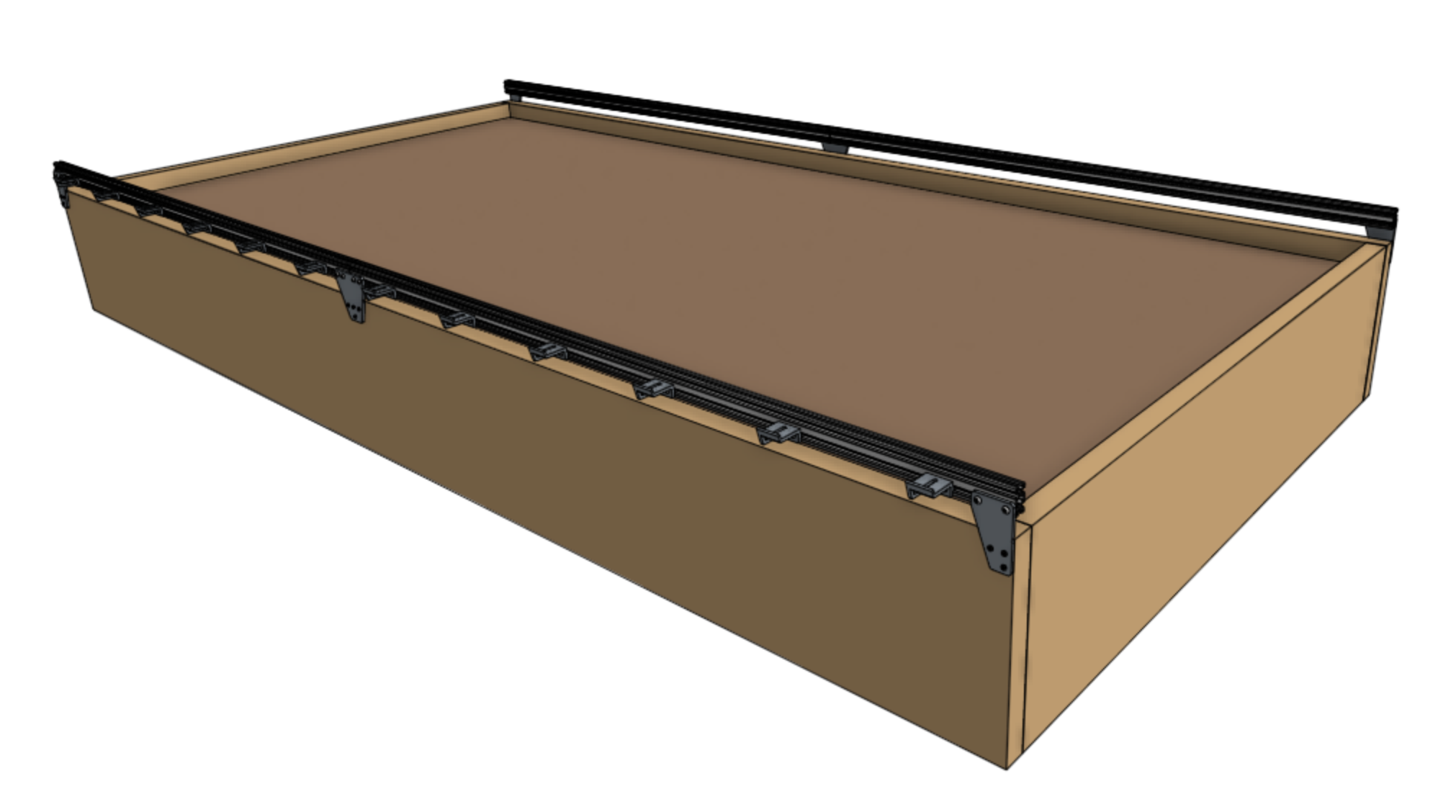
2-12 hours
This is the estimated time it will take to assemble the tracks, mostly dependent on which size kit you have.
The two tracks must be a parallel distance apart between 0.5m and 1.5m for Genesis, and 1.5m and 3m for Genesis XL and Genesis MAX so that the gantry may span the distance between them. Tracks may be spaced closer together than the maximum, in which case you may consider cutting the gantry main beam so that it does not inconveniently extend beyond the tracks.
Shortening the tracks
The easiest way to shorten the tracks is to remove extrusions. Should you want an overall track length different than the 1.5m increments the extrusions afford, then you will need to use a hacksaw or bandsaw to cut the extrusions to your desired length. You can shorten your tracks to a minimum length of around 0.5m.
Lengthening the tracks
If you would like to extend your tracks, you will need additional extrusions, track joining plates, cable carrier supports, and hardware, as well as longer x-axis cable carrier, belt, wiring, and tubing.
For serious hackers and DIYers only
We do not currently sell extension hardware, offer kits with tracks longer than 18m, or provide support for kits that are modified in this way.
Lengthening the tracks beyond what is included with your kit may introduce significant unforeseen problems to your FarmBot. If you decide to extend your tracks you will need to purchase and/or make the additional components on your own and troubleshoot any problems you run into. You may seek support in the community forum.
Step 1: Lay out the track extrusions
Handle with care
The aluminum extrusions may have sharp corners and edges.
Lay out all of the track extrusions in the location that you want to attach them to your supporting infrastructure. Make sure that extrusions are fully butted against each other. This will help you attach the plates in the correct location.
Overhang is a-ok
The ends of your tracks do not have to match up perfectly with the ends of your supporting infrastructure. A little overhang or coming up short (when working with a raised bed) is just fine.
Step 2: Attach the horizontal cable carrier supports
Attach six 40mm horizontal cable carrier supports to the lower slot of a track extrusion using 40mm nut bars and M5 x 10mm screws. The supports should be spaced evenly along the length of the extrusion, and they should be attached to the track extrusions on the side of the bed that you intend to be the left side of the FarmBot (when looking from the front).
Repeat for all of the track extrusions on the side of the bed that will eventually have the electronics box (two extrusions total for Genesis, four for Genesis XL, and 12 for Genesis MAX).
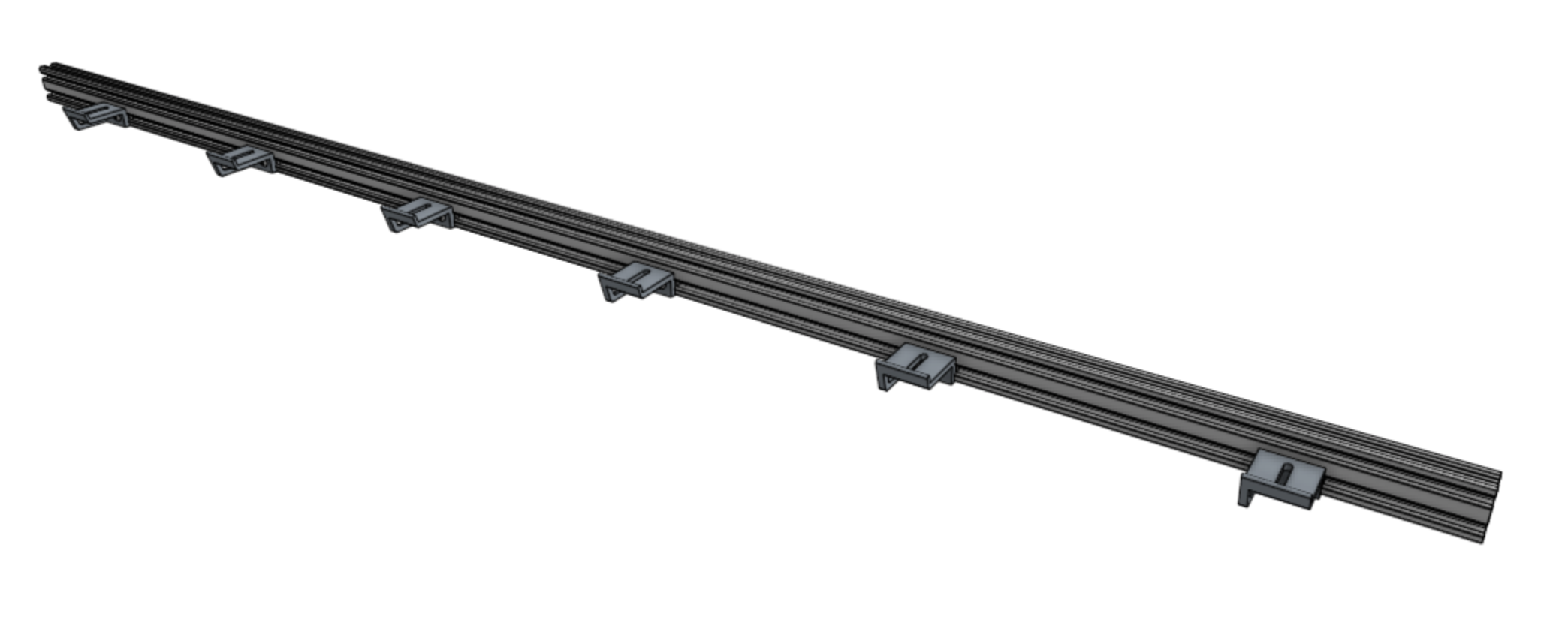
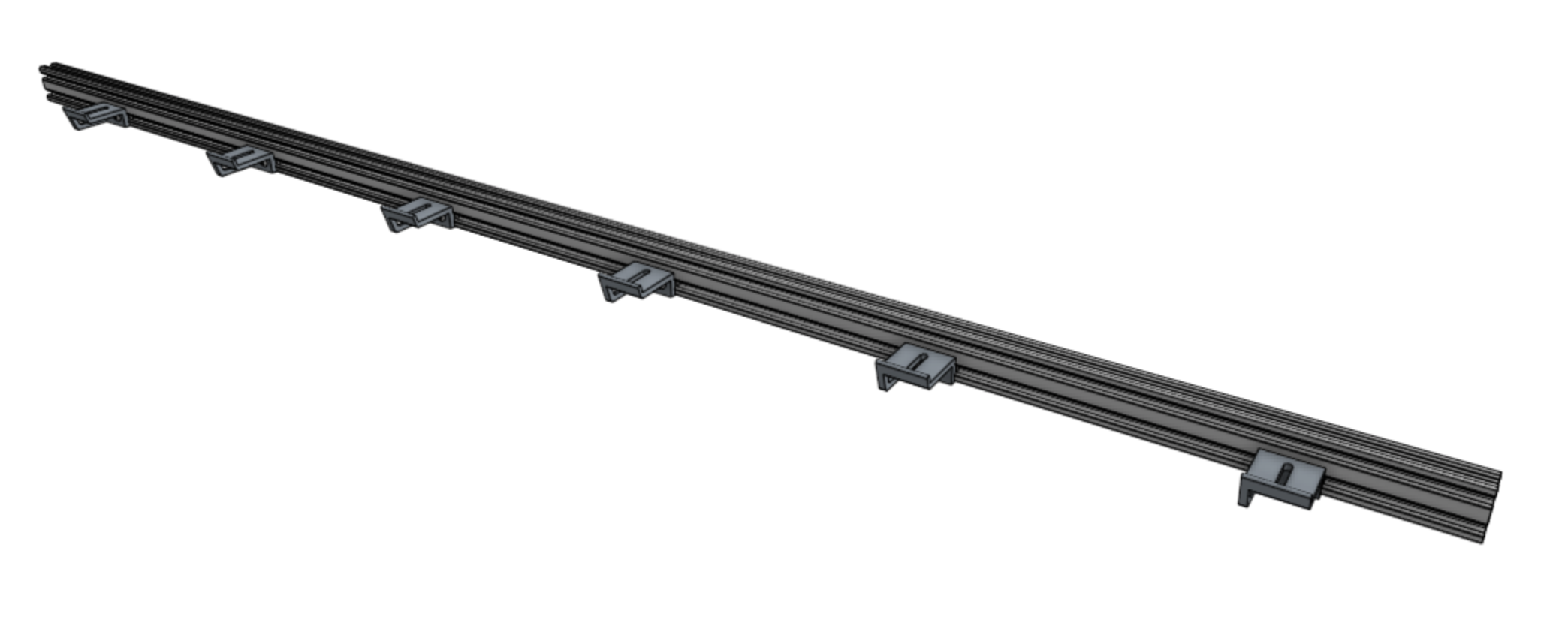
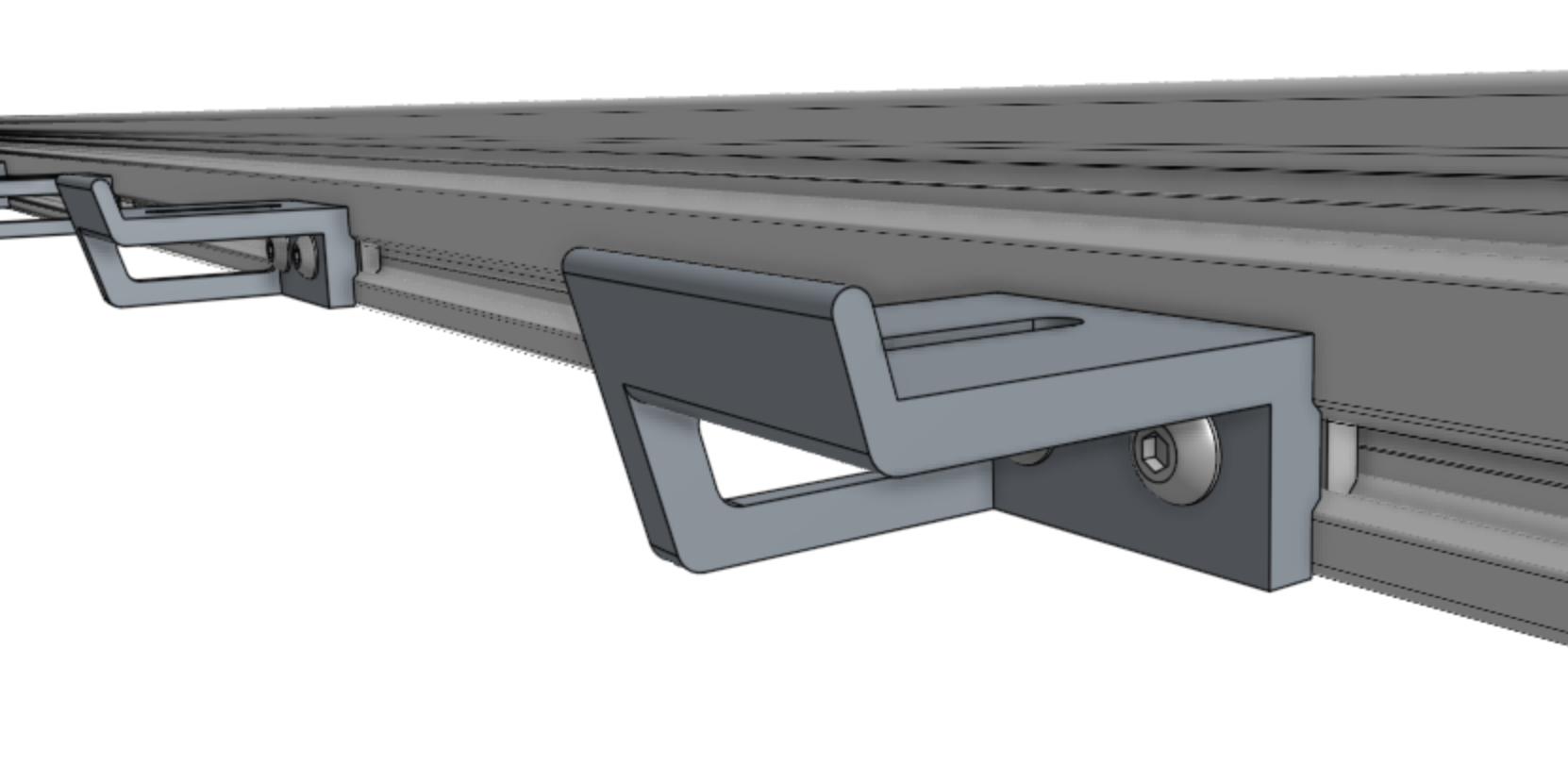
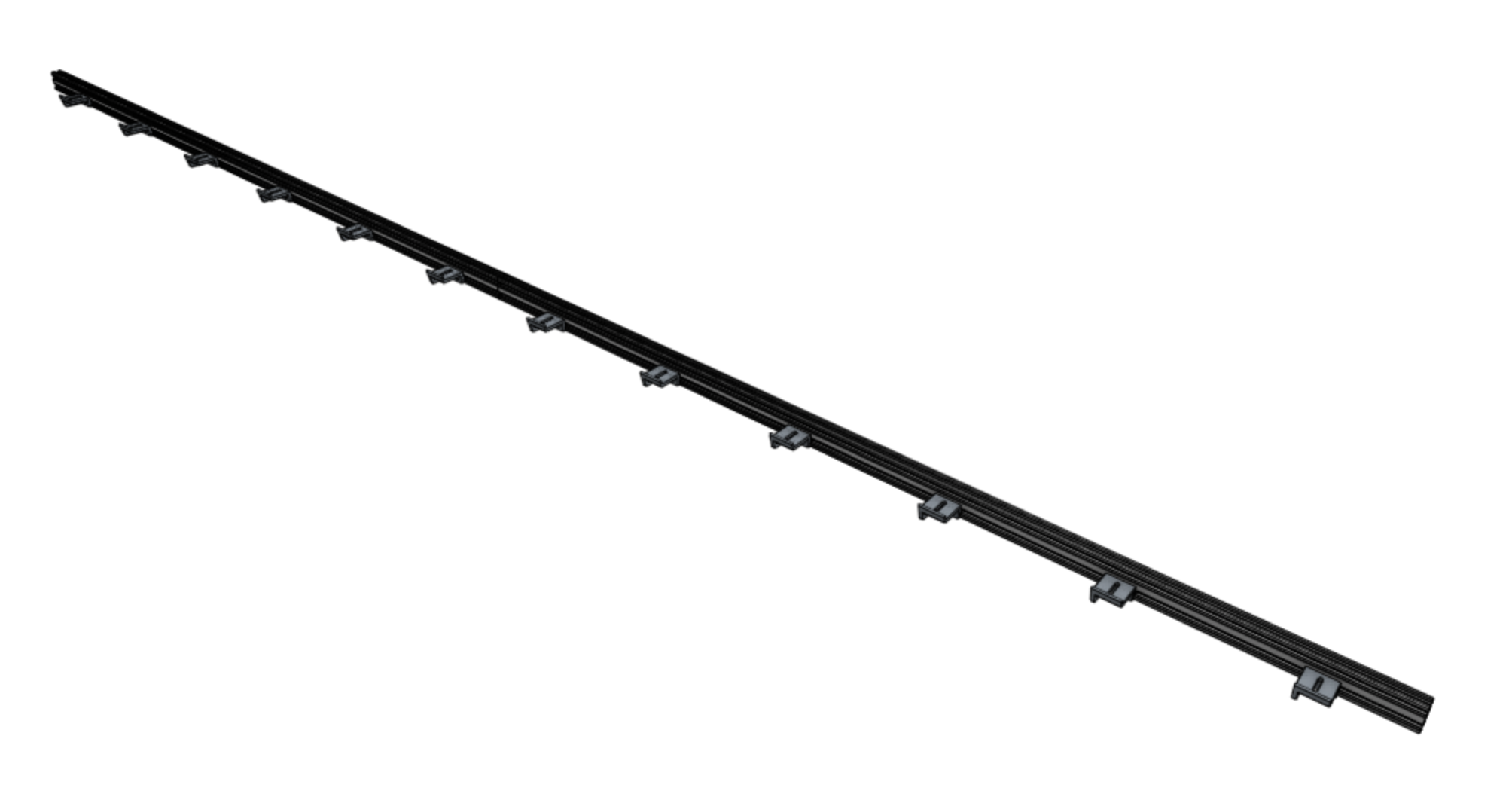
Step 3: Attach a track end plate
Position a track end plate as shown below and screw it into the supporting infrastructure with three wood screws.
Vertically aligned
Use the small notches in the track end plates and track joining plates to help position the plates with perfect vertical alignment with respect to your supporting infrastructure and each other. You should only use these notches if the top edge of your supporting infrastructure is level and straight.
If the top edge of your supporting infrastructure is not level or straight, then you will need to manually ensure that your track plates are vertically aligned with other means. Because the gantry has wheels that ride on the bottom face of the track extrusions, you need to ensure that the bottom of the track extrusion will be at least 25mm away from the top of the supporting infrastructure so that the wheels have adequate clearance.
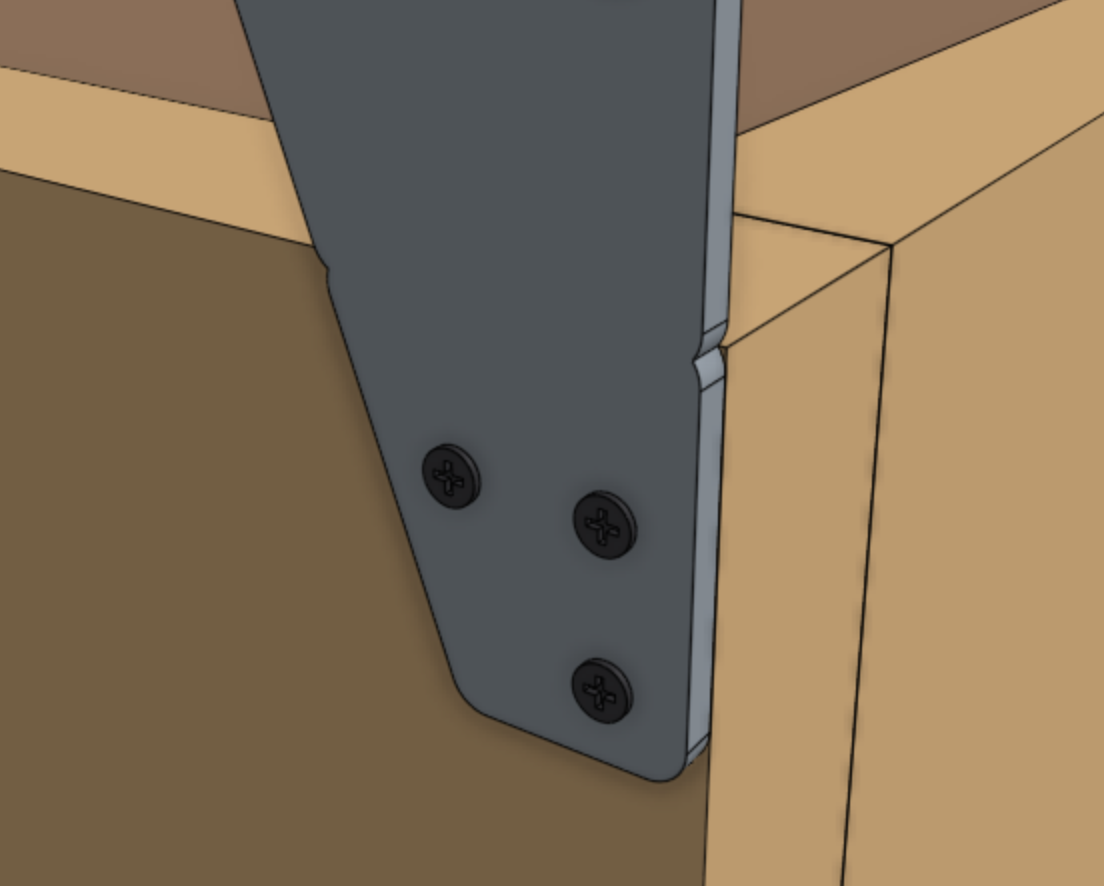
Step 4: Attach a track joining plate
Position a track joining plate such that one half of it will be able to attach to each track extrusion and so that it is vertically aligned with the first track end plate. Screw the plate into the supporting infrastructure with four wood screws.
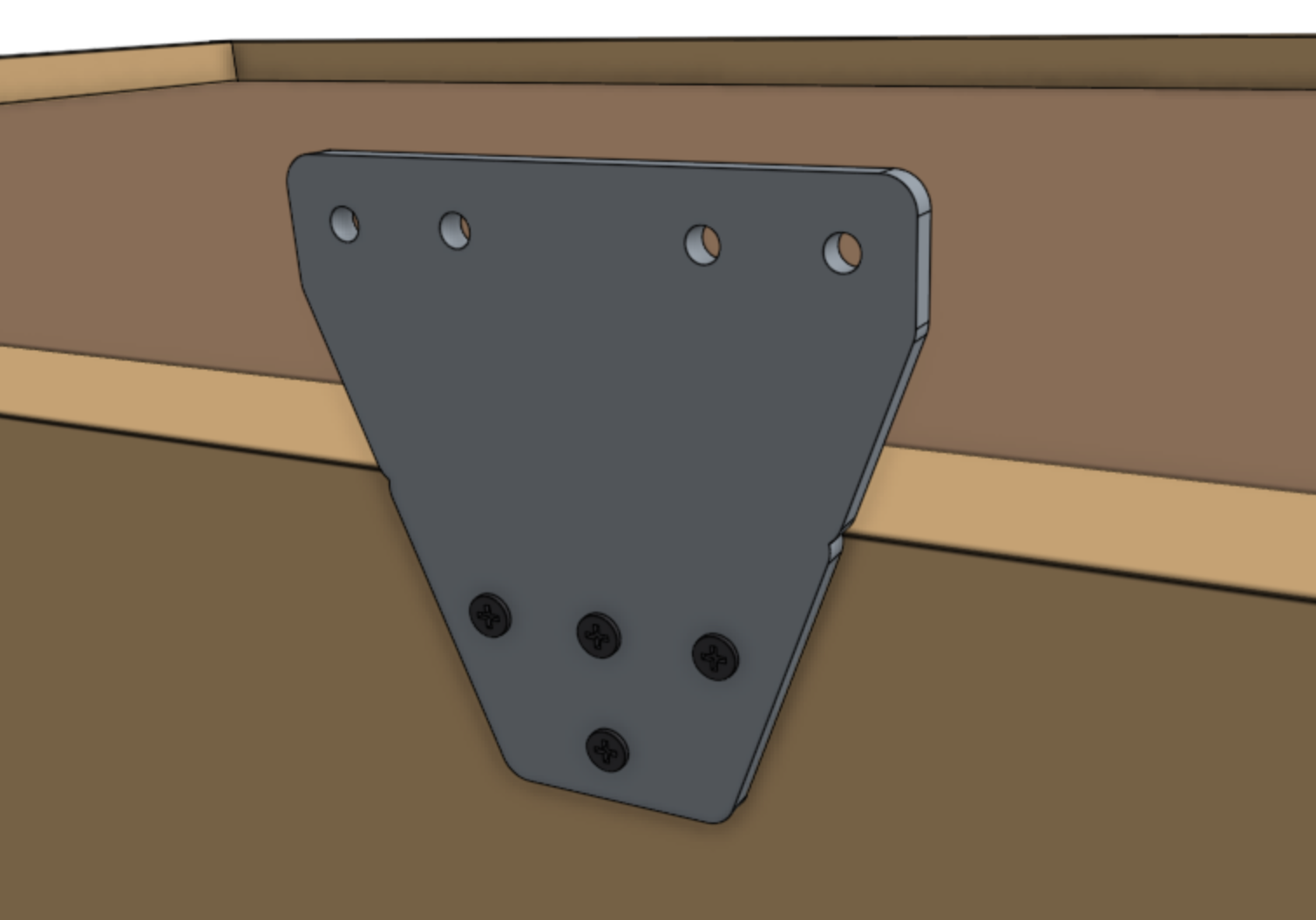
Step 5: Attach the first track extrusion
Attach one end of the first track extrusion to the track end plate using a 60mm nut bar and two M5 x 10mm screws.
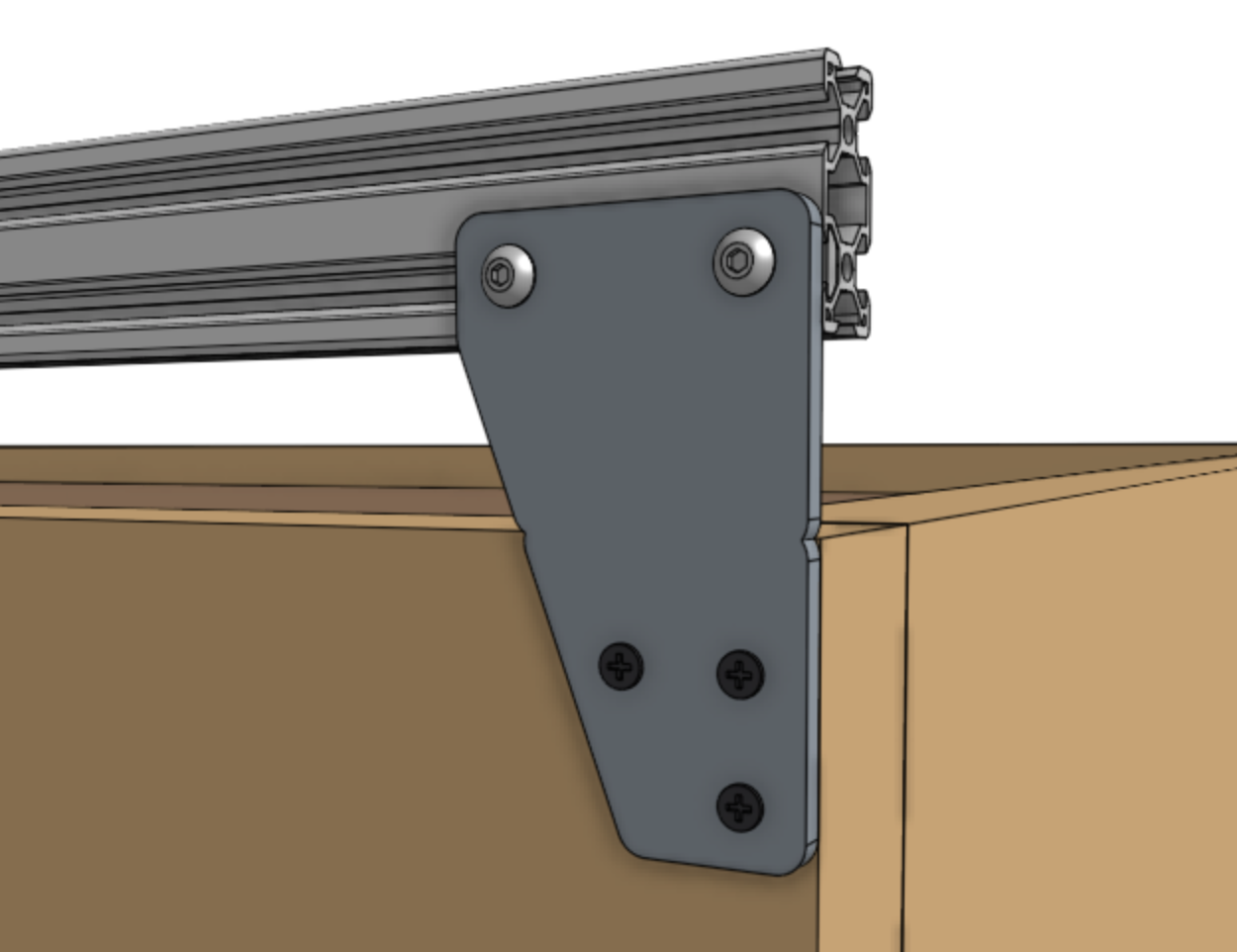
Attach the other end of the extrusion to the track joining plate using a 100mm nut bar and two M5 x 10mm screws. Do not fully tighten the screws on the track joining plate yet.
Your kit may not include 100mm nut bars
If your kit was shipped before November of 2020, it does not include 100mm nut bars. Instead, use 40mm nut bars to attach the track extrusion to the track joining plate.
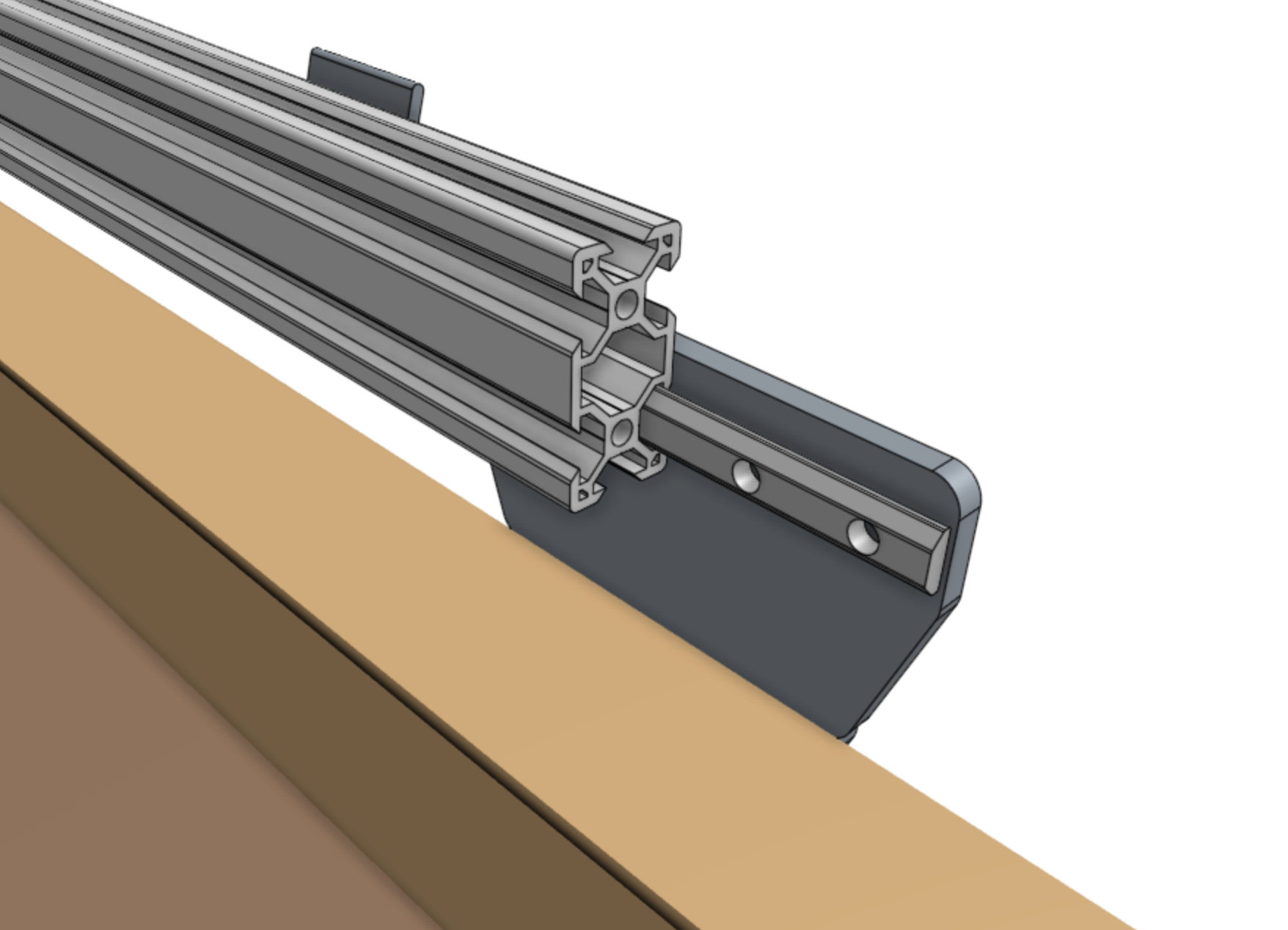
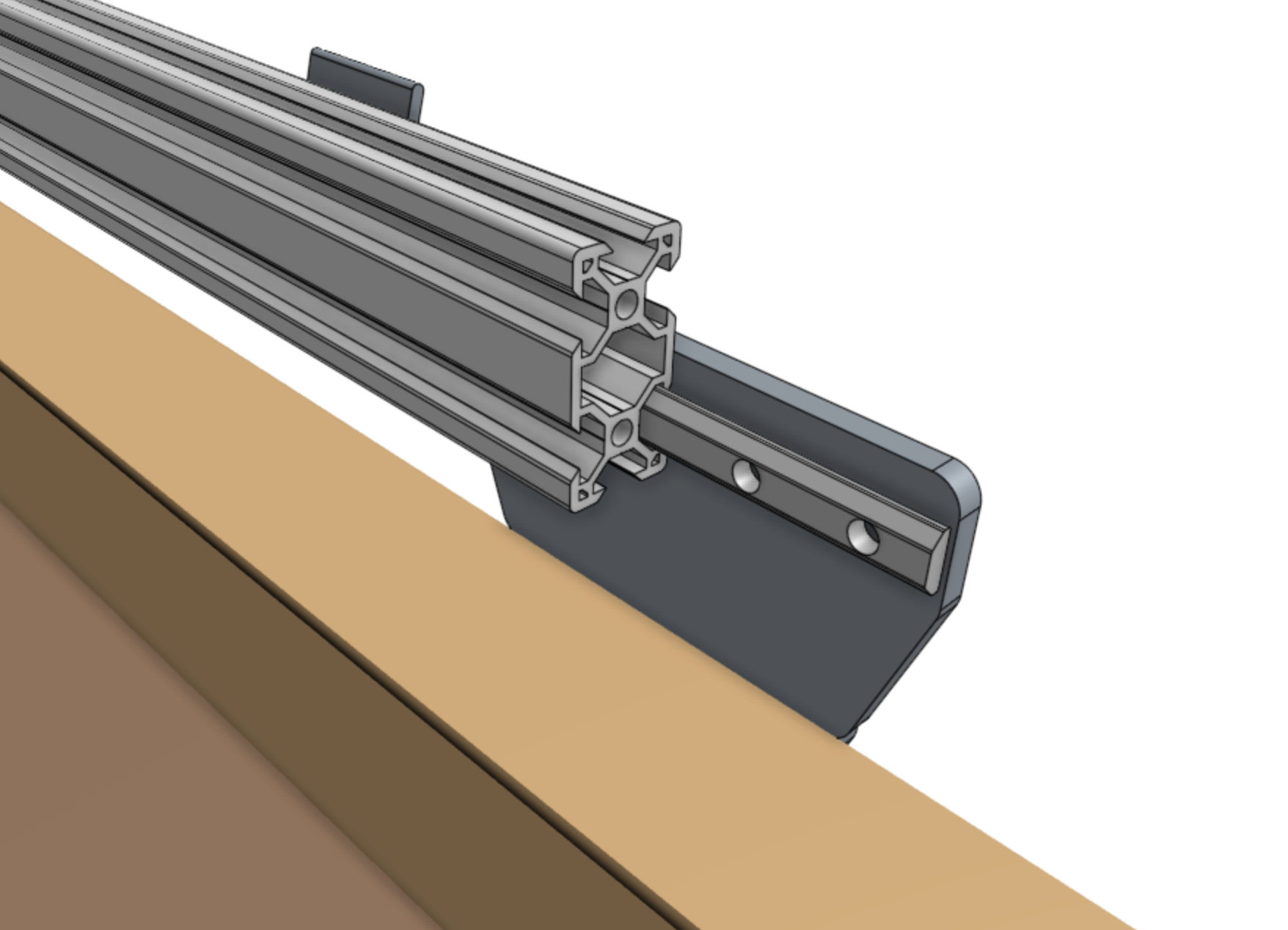
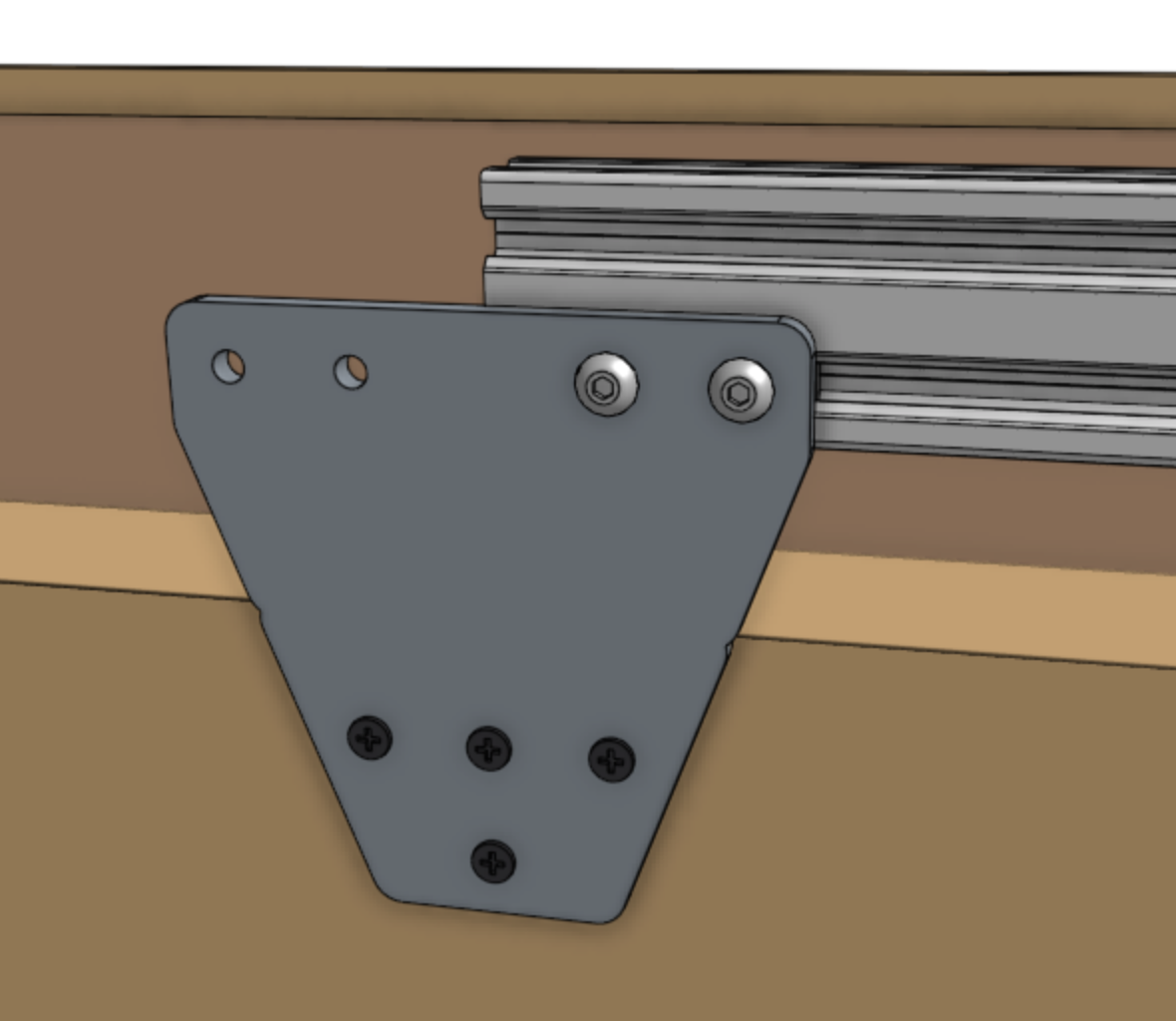
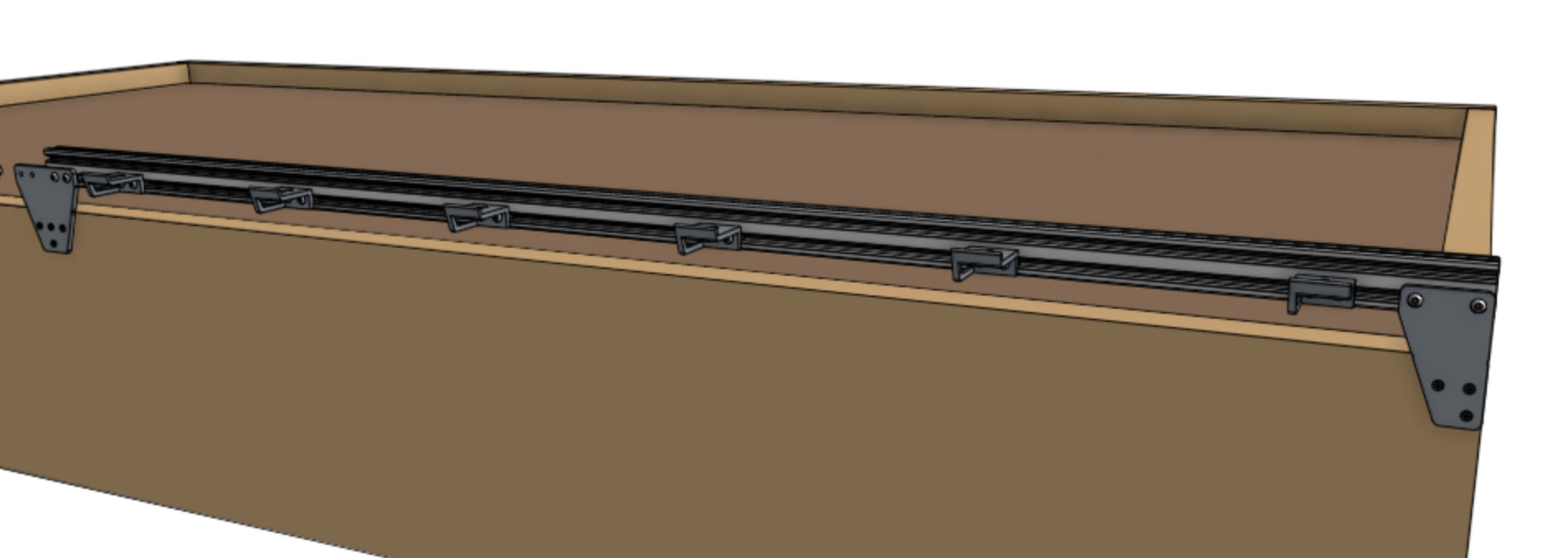
Step 6: Attach the next extrusion
Slide the lower V-slot of the second track extrusion onto the 100mm nut bar. If it does not slide on easily, you may need to loosen the screws holding the first extrusion in place.
If your kit is from before November 2020, use a 40mm nut bar instead.
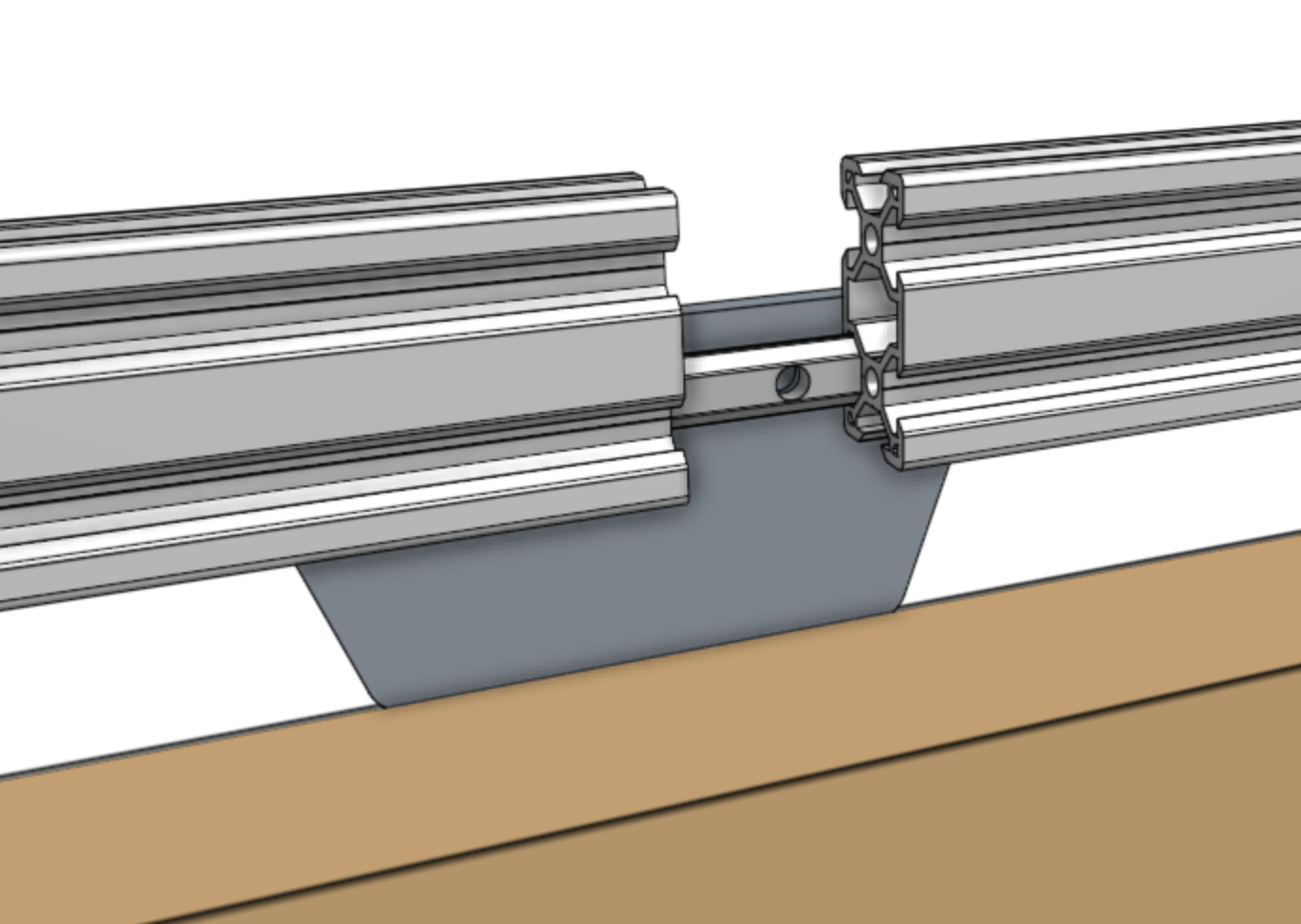
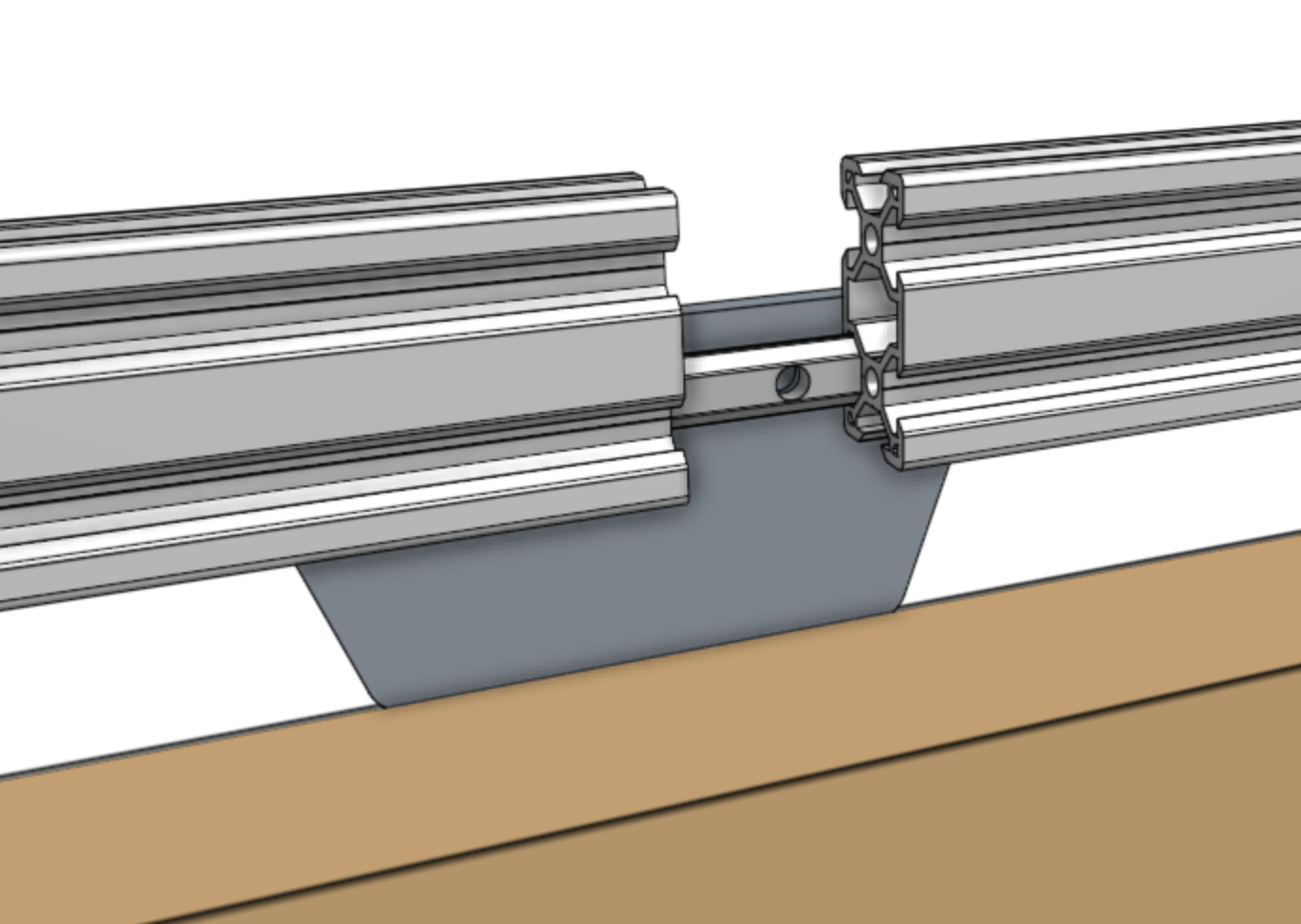
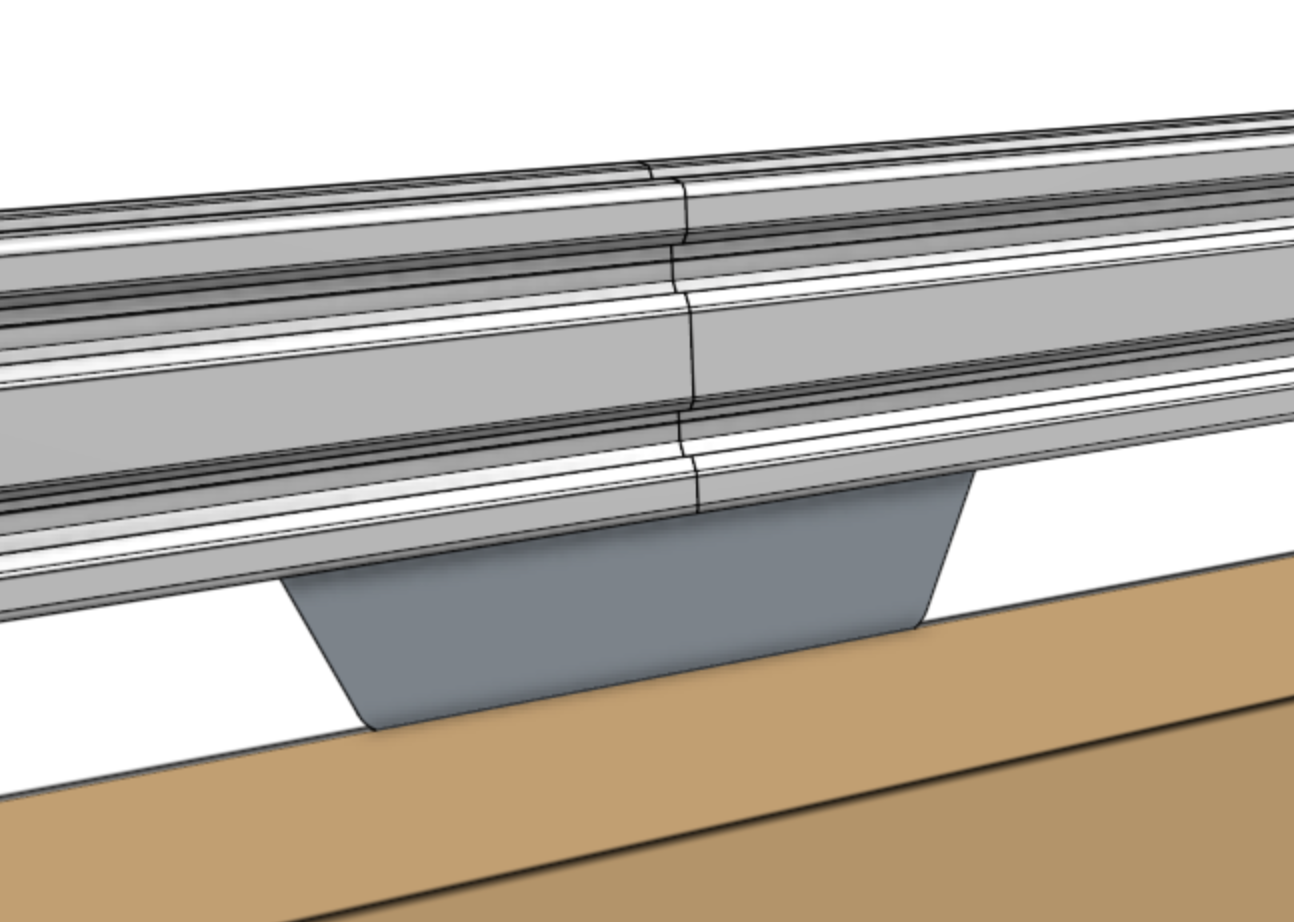
Push the second extrusion into place so there is no gap between the extrusions, then add two M5 x 10mm screws.
Extrusion alignment is key
Ensure the track extrusions are positioned tightly together at the middle of the track joining plate. The top and bottom of the extrusions must be flush so that the gantry can move across the tracks smoothly. Ensure that your extrusions are parallel (no kink where they meet) by looking down the length of the tracks. If there is a kink, adjust the track extrusions and plates accordingly.

Support the free end
At this time the 100mm nut bar will be keeping the two extrusions aligned. Avoid moving the free end of the second extrusion in a way that would cause misalignment, otherwise you risk bending the nut bar. You may wish to use a piece of wood or have someone help to support the free end of the extrusion while you prepare for the next step.
Step 7: Attach the next track joining plate
This step applies to XL and MAX kits only
If you have a standard sized Genesis kit (3m long), proceed to the next step.
Position another track joining plate such that one half of it will be able to attach to the free end of the track extrusion that was just put in place, and so that it is vertically aligned with the other track mounting plates. Screw the plate into the supporting infrastructure with four wood screws, and then secure the extrusion with another 100mm nut bar and tighten all screws.
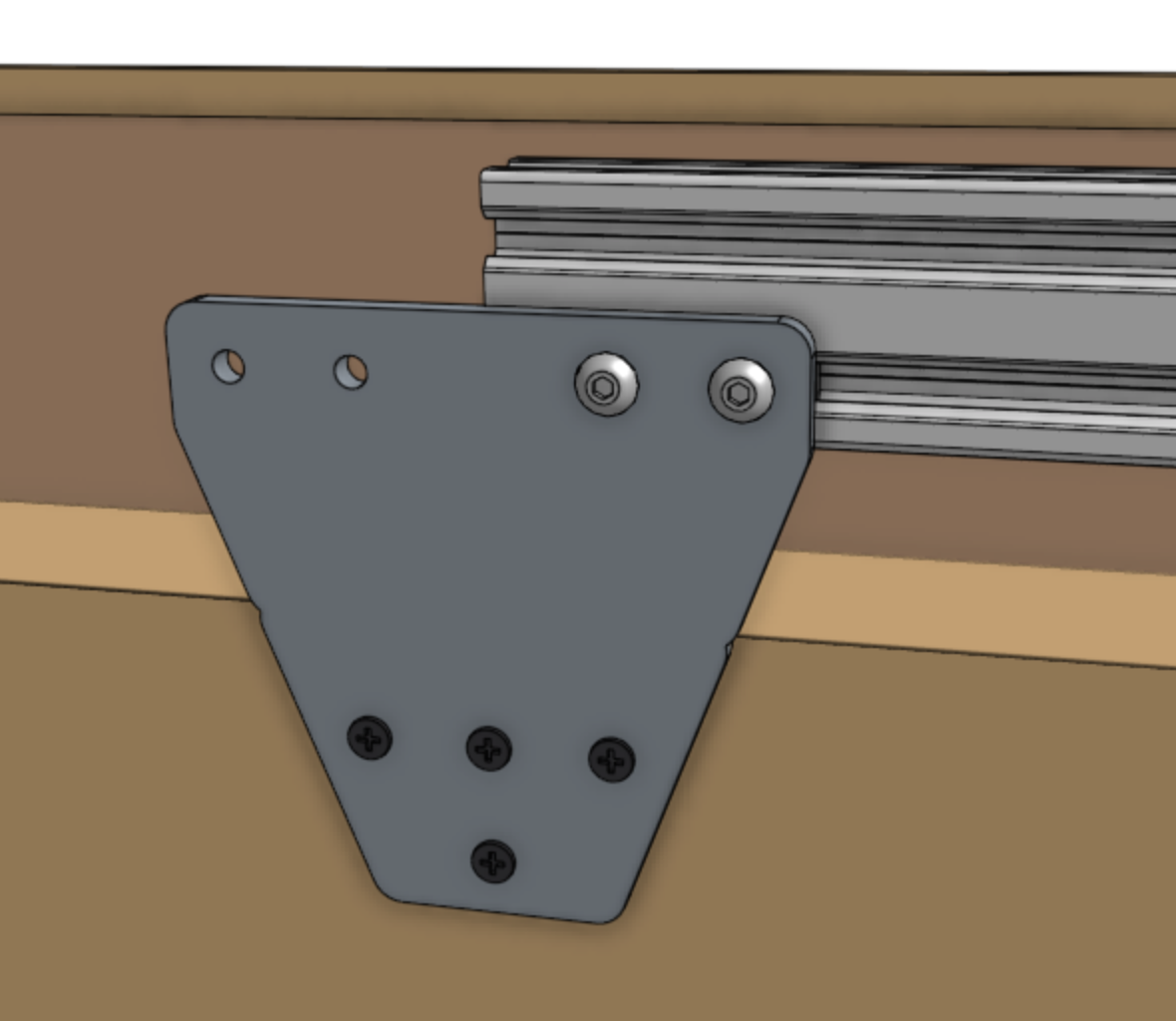
Repeat to install subsequent track joining plates and track extrusions.
Step 8: Attach the second track end plate
Position the second track end plate and secure it to the supporting infrastructure with three wood screws. Then fasten the final track extrusion to the plate using a 60mm nut bar and M5 x 10mm screws.
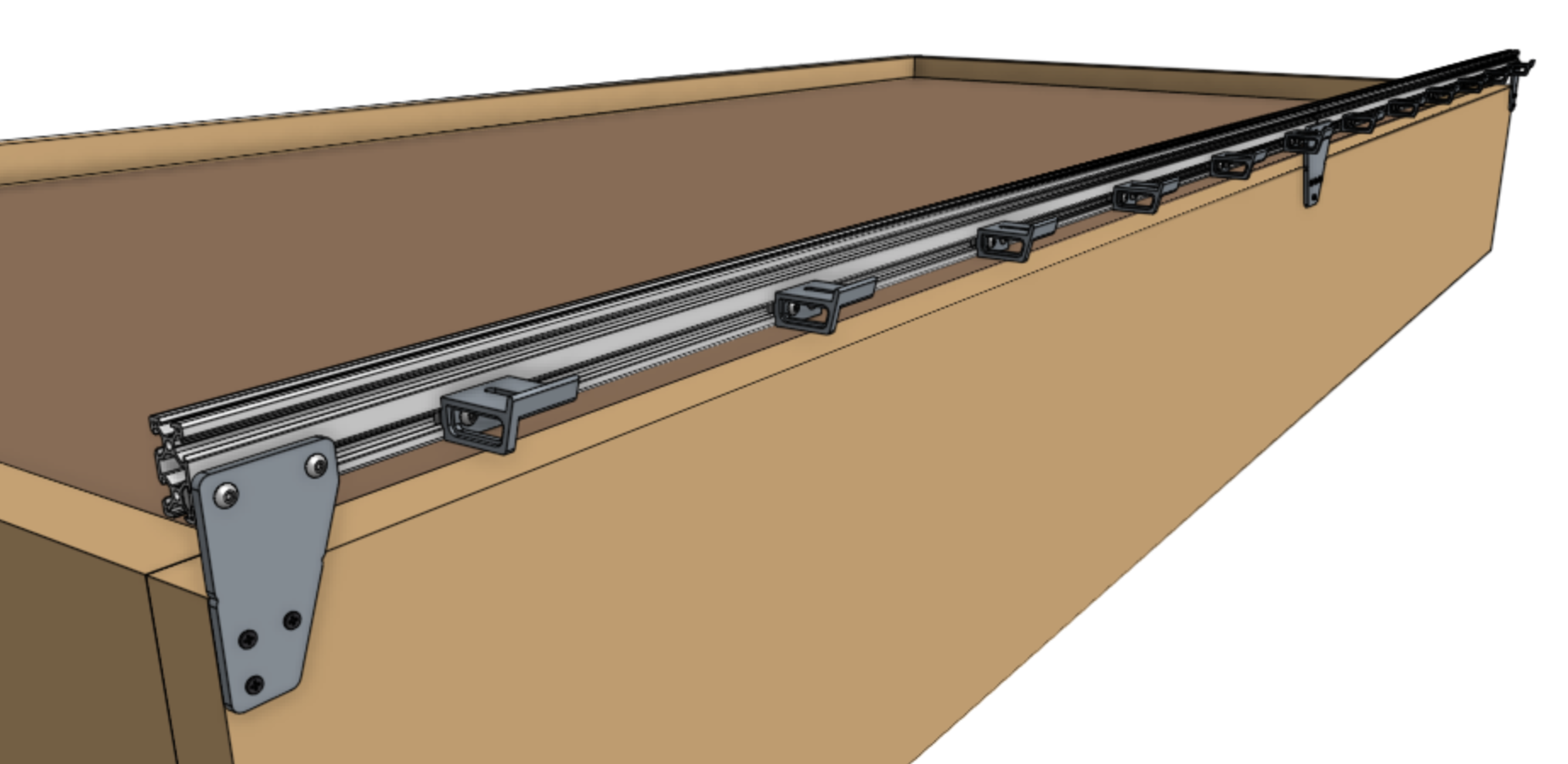
Step 9: Install the other track
Repeat steps 3 through 8 for the track on the other side of the bed. Note that the second track will not have any horizontal cable carrier supports.
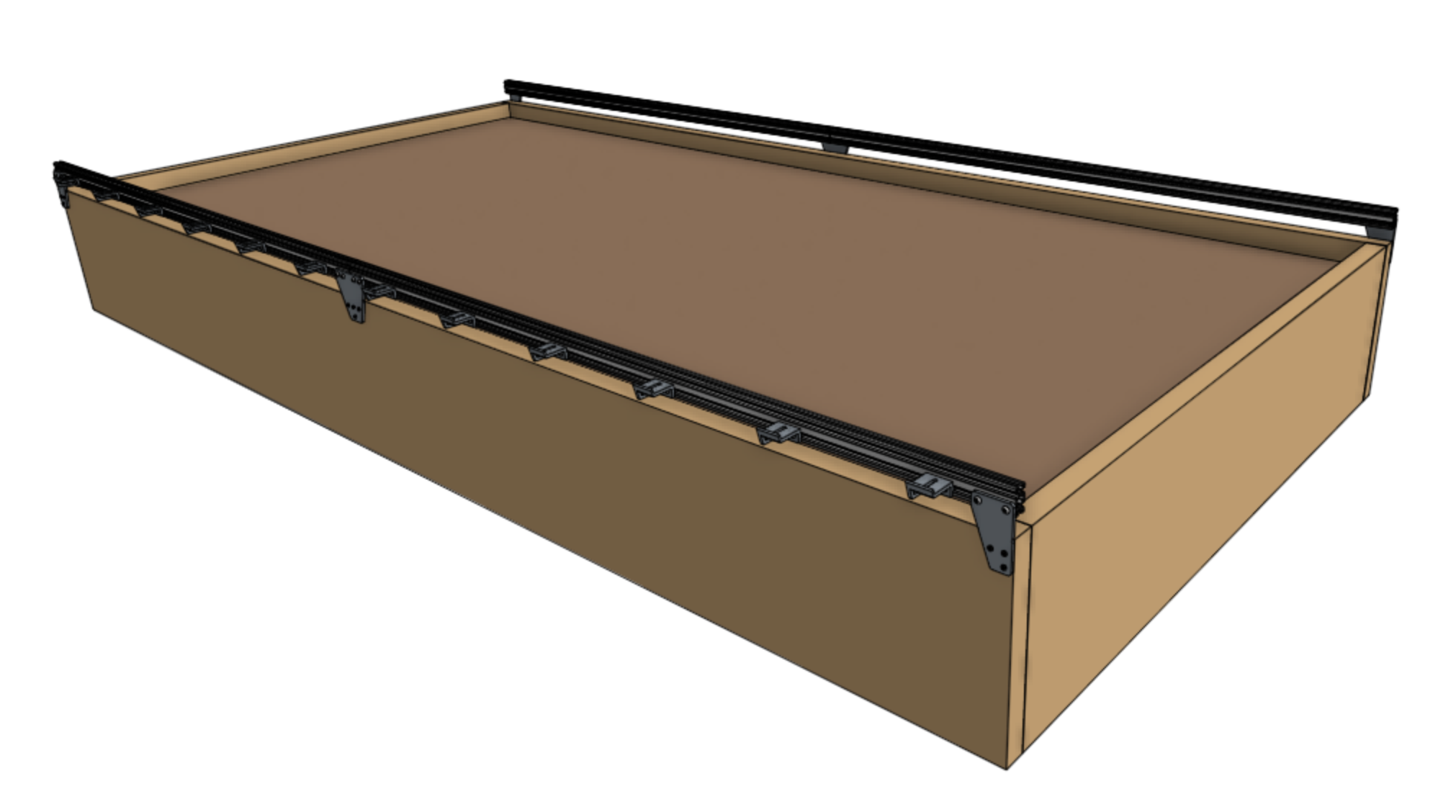
Parellel or bust
It is critical that the distance between the two tracks is consistent. If it is not, there will be harmful forces placed on the gantry and tracks as the gantry moves across the non-parallel tracks.
You can use shims or other spacers to better align track plates in case your supporting infrastructure is not perfect.
Step 10: Sand away bumps
If needed, use 150 grit sand paper to sand away any bumps on the diagonal surfaces of the extrusions that the FarmBot wheels ride upon. This will ease the movements of the FarmBot and improve longevity. Make sure that both the upper surfaces and lower surfaces are smooth to the touch and that there is no bump or uneven edges in the transition from one extrusion to another.
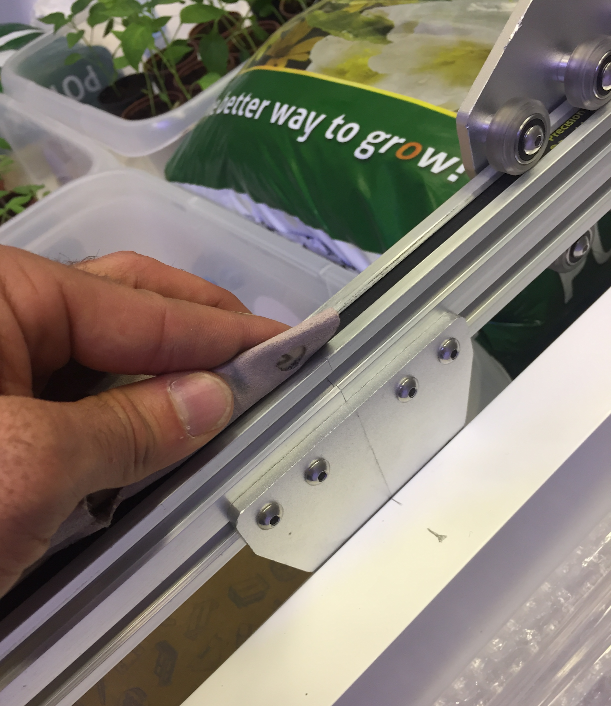
This photo shows that the aluminum tracks can be sanded down so that there is no bump on the transition between one section of track to another.
Woo hoo!
You’ve just finished installing your FarmBot’s tracks - arguably one of the most difficult parts of setting up your device
Onward!